シャープな粒度分布で粒子径を制御した球状のシリカ微粒子、高品質が要求される電子材料分野に幅広く対応
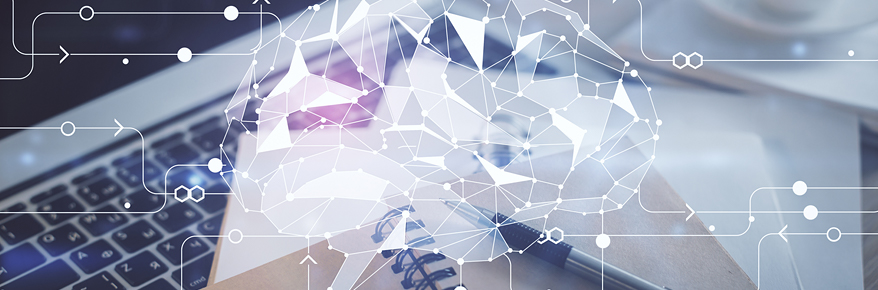
日本触媒の粒子径がコントロールされた真球状のシリカ微粒子はこうして誕生した!
日本触媒の世界に誇れる主要な技術の1つに、微粒子技術があります。
ナノサイズからミクロンサイズまで様々な粒子径の微粒子を無機系、有機系、有機無機複合系と幅広い素材でラインアップしています。
その中で、1987年の製品化以来、長く、日本触媒の微粒子製品の中心的存在であったシーホスター®KEの開発ストーリーを紹介します。
大手PETフイルムメーカーのニーズから始まった研究
1985年 中央研究所第5研究室では、自社製品のラインアップにない無機系材料の微粒子技術の開発に取り組んでいました。
ある日、大手PET(ポリエチレンテレフタレート)フイルムメーカーを訪問して微粒子の開発品を紹介していた時に、先方の担当者から「ところで、日触さんの技術で、シリカの球状微粒子ができないですか?」と質問されました。
先方では、記録媒体(磁気テープ)用ベースフィルムの滑り剤を探していて、粒度のそろったシリカ(二酸化ケイ素)の球状微粒子を探しているとのことでした。
当時は球状で粒度のそろったシリカ微粒子はなく、従来のシリカ微粒子では性能が不十分とのことでした。
早速、会社に戻り、シリカ微粒子の合成技術について調査したメンバーは、アメリカのシュテーバーらの研究による1968年の論文を見つけ、この技術をもとに実験を開始しました。
確かに、論文のとおり実験してみると、一定の粒度で球状のシリカ微粒子が合成できることがわかりました。しかし、使用する原料物質が非常に高価なものであったため、このまま製品化することは難しかったことから、化学構造の類似した、より安価な原料物質を用いて、実験を行うことにしました。
ここでチームは壁に突き当たってしまいました。この原料物質を使用すると、原料の加水分解速度が早すぎるため、粒子のサイズが一定のところで止まってしまい、それ以上大きなサイズの粒子がどうしても合成できなかったのです。
しかし、実験を繰り返し、反応条件や装置など様々な工夫を重ねて、やっとPETフイルムメーカーが要望される種々の粒子径をコントロールすることが可能となり、1987年に当社ではじめてとなる無機系微粒子製品であるシーホスター®KE-Eタイプが製品化されました。
当時の主要メンバーであったTさんは、
「ニーズをくれたPETメーカーは、シリカ微粒子製品の供給をすぐに始めて欲しいと強く希望していました。そのスケジュールに答えるため、ラボからベンチ、パイロットとスケールアップ作業は、うちのチームだけではとても人手が足らず、入れ替わりで他の研究室の研究員が応援に来てくれて、助けてもらいながら、必死に取り組みました。ベンチ設備に使用する反応釜も新品を調達する時間がなく、遊休品のあり合わせの転用だったので、不純物の混入を防ぐため、紙やすりで釜の表面を自分で研磨して使用したんですよ」と懐かしく振り返っています。
拡販のために、用途展開を目指したが大きな需要はなく
大手PETフイルムメーカーでの採用で製品化ができたものの、エチレングリコール分散体であるEタイプは、需要のほとんどがPETフィルム向けでした。
そこで、チームでは拡販のために、シーホスター®KEの粉体化の検討を行い、1989年に微粒子粉体であるシーホスター®KE-Pタイプを開発しました。
この粉体化により、シーホスター®KEはあらゆる樹脂への添加が可能となり、様々な分野の顧客からサンプル要求が来るようになりました。
シーホスター®KEの開発は、1992年に吹田研究から姫路製造所の技術課に移管されましたが、製品として販売を継続するか議論される対象になっていました。
実は、シーホスター®KE-Pタイプの開発により、確かに様々な顧客に注目はしてもらえたものの、期待していたような大きな需要につながる案件はでてこなかったのです。この状況を打開するため、特に高品質な電子材料向けを狙った高純度のシーホスター®KE-Sを開発し、1999年に市場に打って出るも、新規顧客の開拓にはつながらず、販売数量は伸び悩み、益々、事業の継続の岐路に立たされる状態に追い込まれて行きました。
世界の液晶ディスプレイの需要拡大に合わせて、ついにブレイク!
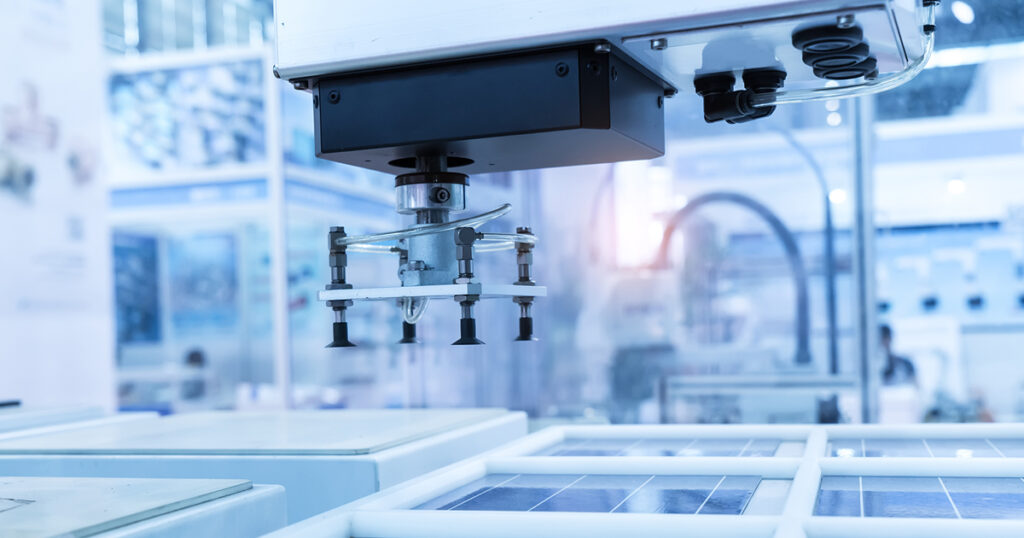
2000年頃から液晶ディスプレイが注目される中、より大きなサイズの液晶パネルのニーズが急激に高まってきました。この液晶パネルの大型化に際し、液晶パネルへの液晶の注入方式が大きな課題の一つでした。従来の液晶パネルへ液晶を注入する方法では、液晶パネルのサイズが大きくなるにつれ、液晶を均一、短時間に注入するのが難しくなっていました。そういった中、液晶ディスプレイ業界では、ODF(ワン・ドロップ・フィル)工法という画期的な工法が実用化されました。
一方で、ODF工法で使用する液晶シール剤には課題がありました。充填剤としてシリカ粒子を使用するのですが、そこで要求される品質を満足する量産化されたシリカ粒子がなく、当社に白羽の矢が立ったのです。
当社はシール剤メーカーからシーホスター®の引き合いを受け、開発品を納入しましたが、電子顕微鏡でしか確認できない微小異物の混入を指摘され、原因究明と対策に追われました。また、量産確立を並行して行う必要があり、メンバーは目まぐるしい日々を送っていました。それでも、関係者の知恵と工夫でなんとか乗り切り、顧客と協力して製品中の異物の管理方法なども確立し、何とか供給を継続できました。
当時、主要メンバーであったSさんは、振り返って、
「世界的に大型液晶ディスプレイの生産が急拡大しており、顧客からもシーホスター®の受注が急増していました。当社からの供給を切らすと世界の液晶ディスプレイ生産ラインが止まるので何とか必要量を供給して欲しいと顧客から懇願され、メンバーは必死で対応しました。でも、要求された品質のものを要求された量で供給できるのは、世界で当社だけでしたので、メンバー全員、使命感を持って改良と製品の供給に取り組んでいたと思います」と話してくれました。
研究者たちの真摯な思いで成功した製品
Tさんは、シーホスター®KEの開発について、次のように回顧しています。
「短期間で製品化までこぎつけても、このテーマに対する研究所の上層部の風当たりは強かったんです。その理由として、そもそも文献の公知技術が基本となっていること、製品に自社原料を使用していないことで、他社との差別化や競争力がないだろうと言われていました」
しかし、開発メンバーは、リーダーを中心として、絶対成功させるという熱い思いで取り組みました。
その結果として、1987年の製品化以来、シーホスター®KE-Eは、現在もPETフィルム用途向けへの納入が続いています。
さらに、事業継続が危ぶまれた時期も、担当者がシーホスター®に惚れ込み、絶対に世の中の役に立つ場面が来ると信じて、ついに、液晶ディスプレイの製造工程の大変革という場面にマッチすることができました。
そこに、お客様のニーズがあり、それに真摯に答えるために取り組む技術者の思いが、シーホスター®KEの成功に結びついたのです。
当社の微粒子技術は、プラスチックフィルムのアンチブロッキング剤や滑り性向上剤、液晶パネルの光学フィルムやLED用の光拡散剤、複写機のトナー、樹脂の充填剤など様々な分野に貢献しています。
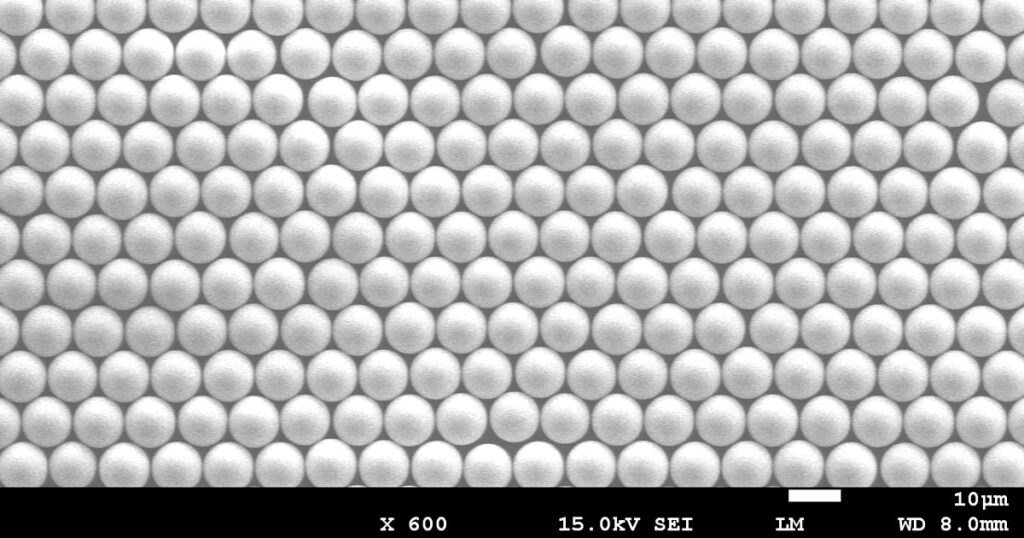