世界トップシェアの高吸水性樹脂、40年つづく創意工夫のバトン
コミュニケーションの工夫からAI活用まで、製造所で進む安定供給強化への取り組み
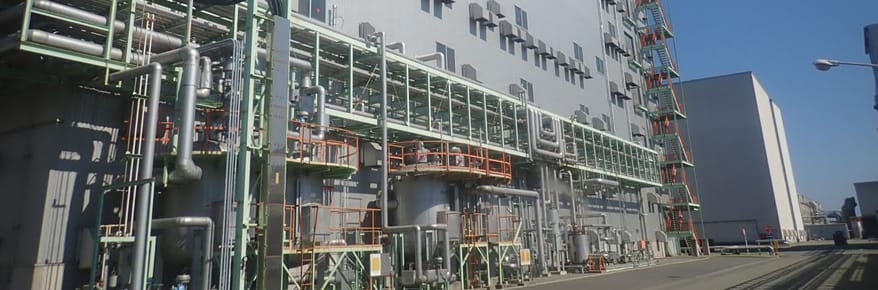
日本触媒の主力製品である高吸水性樹脂(以下、SAP)。自重の数百倍~数千倍の水を吸収する特性から、紙おむつなどサニタリー製品や保冷剤、カイロ、さらには園芸用の保水材などの原料として幅広い分野で社会に貢献して、世界トップシェアを占めています。
そんなSAPが事業化されたのは1983年のこと。そこから40年もの間、生産・品質の技術改良を続けながら、顧客ニーズに応える形で多品種のSAPを提供し続けています。そして、SAPの性能・品質を支え、世界中に製品を輸出し、日本触媒で最も生産能力を持つ主力製造所が姫路製造所です。
姫路製造所は青く映える瀬戸内海に面した、90万m2(東京ドーム約19個分)という広大な面積を持つ製造所。SAPの原料であるアクリル酸から一貫製造を行っています。1000名を超える従業員が、日々安全に配慮しながら主力製品の生産を行っています。
SAPの安定供給が使命。そのために「多くの経験に加えて、データ活用も推進」
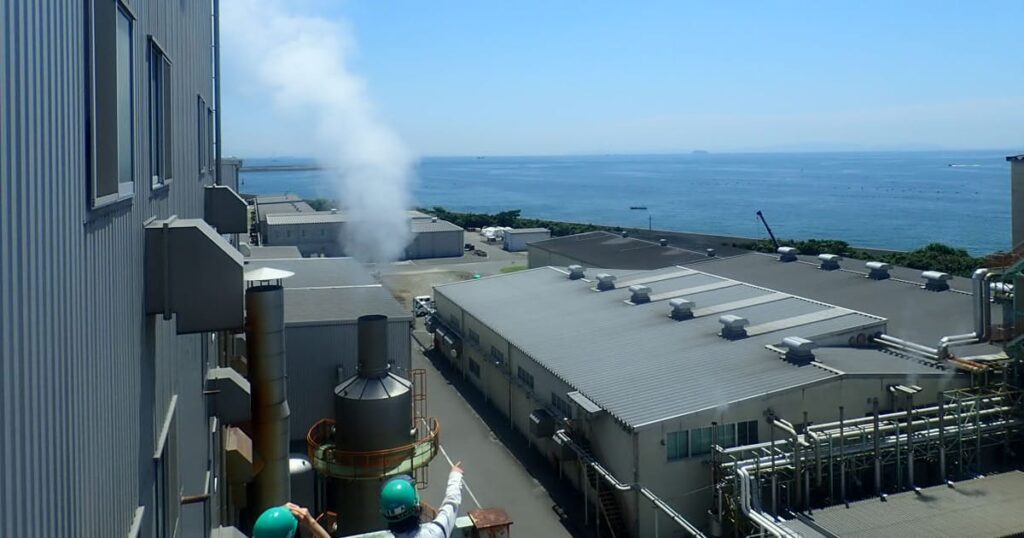
吸水性樹脂製造部で、SAPの保全業務や新製品の立ち上げなど、重要な役割を担う部署で活躍する3名の中堅技術者に日々の業務の話を聞きました。彼らのミッションは、自動化が進んだ製造プラントの設備の機器類の維持やトラブル時対応、新製品立ち上げにおいて必要な設備を構築することです。
「複数ラインのメンテナンスを行っていると、ずっと見ているからなのか愛着が出てきて、飼育員のような気分になることがあります」と語ってくれるのは30代のMさん。Mさんは、入社以降SAP一筋、情熱派と評判の技術者です。
SAPは多段階で複雑な製造工程を経て作られます。原料の調整から製品の充填まで1つ1つの工程で細かく温度や条件が制御されることから、各所で多くの調整やスケジュールの更新が必要となります。
「『このラインでは、このようなことが起きる傾向』と自分の勘を元に感覚的に判断するだけではなく、過去データを確認することも大事にしています。モノの安定供給が何より大事なミッションなので、トラブル時の判断に悩むこともありますね」と、仕事に取り組む姿勢を語ってくれました。
もう一人の担当者Kさんも話します。
「お客様からの様々な要望に応えるために製造時の優先順位が変わりやすく、突発的なトラブルに対応することも…。製品の製造を優先したいと思いますが、保全活動も大事なことなので、都度何を優先すべきか的確な判断が求められます。そんな時でも、過去の製造時のデータに基づいて議論できるようにしています」
SAPの製造技術は今も進化。だからこそ日々のコミュニケーションで助け合う
Kさんが続けます。
「SAPは製造工程が複雑で制御する条件が多く難易度が高いですが、まだまだ進化できると思っています。その上、日々安定な製造が必要なため、基本的なチェックリスト管理などだけでは足りないですね。特にコミュニケーションが本当に大事な職場なので、現場で気になることがあれば、若手であっても、どんどん意見を出してほしいと伝えています」
さらに担当者のOさんも語ります。
「『若手にも自分の意見を持ってほしい、意見を言える環境を作りたい』と中堅メンバーで話し合い、試行錯誤しています。最近は、心理的安全性を高めるなど、発言しやすい環境を作るように心がけています。厳しい態度で具体的な指示をするだけでは若いメンバーはついてこないので、こちらから指示を出す前にどう思う?と意見を聞くことも…」
「その甲斐があって、最近はトラブル発生時などに、若手から自発的に『こうしたほうが良いのでは?』」と物おじせずに意見が出ることもあって頼もしいです」と、Oさんは嬉しそうでした。
技術者が引き継いだバトンを、未来のSAP製造につなげて
Mさんは語ります。
「SAPという主力製品に関われていることに誇りを感じます。だからこそ、安定供給のために、新製品導入時には十分テストを行います。図面通りにはいかないですよね、だからこそ早急に新しいことを進めるのではなく、段階的に新しい設備を入れて最適化して。そういうのをちょっとずつ繰り返して・・・。技術や設備も少しずつ新陳代謝されている感じですね」
姫路製造所では、随所に日本触媒の製造技術の新陳代謝が進んでいます。SAPの生産計画にAI(アルゴリズム)を用いた「生産計画最適化ソリューション」を導入した事例を紹介します。
継続的な安定供給のために。熟練者のノウハウをAIに伝承する
「生産計画最適化ソリューション」導入検討時の話を、担当のQさんに聞きました。
「SAP製造は製品ごとに生産条件が異なる上、プラントによって生産可能品目が決まっているなど、制限が多いものです。そのため、生産スケジュール作成は熟練者への属人化が進むなど課題が大きかったです。そろそろ人に頼った作業の限界ではないかとAIの活用を検討し、プロジェクトがスタートしました」
「『是非、進めて欲しい!』と、上層部からの強い後押しも心強かったです。最初の簡易モデル検証時点で強い手ごたえを感じました。人手をしのぐパフォーマンスの可能性が見えたのです」と振り返ります。
プロジェクトは、社内の少数精鋭のコアメンバーがチームワークを発揮し順調に進めることができました。また、社外パートナーにも恵まれた結果、パートナー決定~導入完了まで約1年と短期間での導入を達成できたのです。限られた熟練者が担当していた生産計画のノウハウを、少しずつAI(アルゴリズム)へ移植し、精度を高めていく形で進行しました。
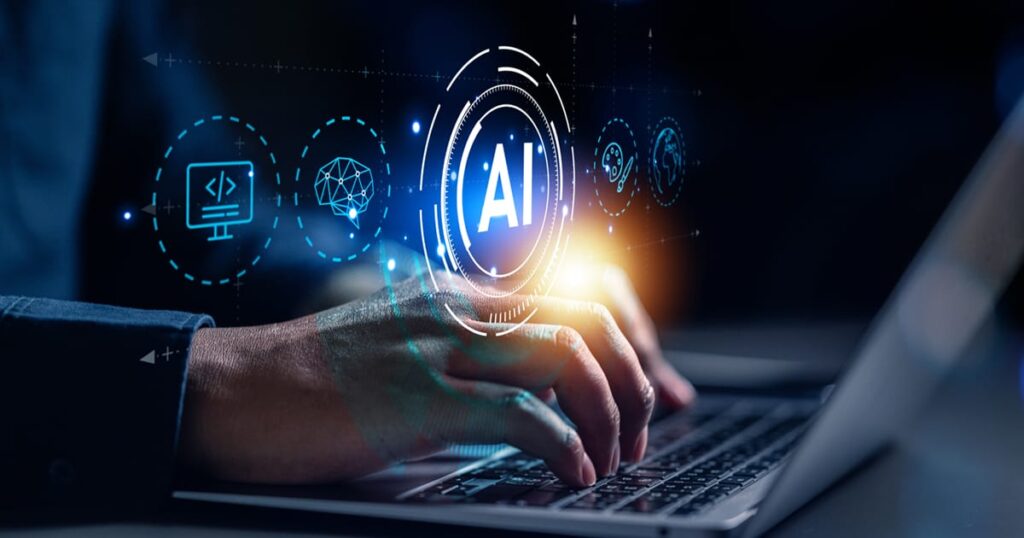
AIが学ぶというよりも、熟練者が新人であるAIに「こういう時は、もっとこうするといいよ」と教え込んでいるかのように見えたという声もありました。AIは条件設定がない部分ではゼロベースで生産計画を行います。そのため、熟練者から見ると思ってもない条件での計画を提案してくることもあり、切替タイミングの決定や倉庫の振り分けなど、自分たちの暗黙知に気づく場面もありました。
AI活用で生産計画作業の効率化に成功。より長期的視点での計画が可能に
各種検討の結果、AI(アルゴリズム)を活用した生産計画最適化ソリューションでは、熟練者が1日がかりで作っていた3か月分の生産計画を、30分で作成できるようになりました。これまで、急なトラブルやリクエストへの対応に人手では直近の計画を組みなおすことが精いっぱいでしたが、長期的な視点で計画を組みなおすことができるようにもなったのです。
Qさんは「SAPは特に顧客数が多く、急なリクエストが入ることもあります。生産計画の変更はあって当たり前、それを前提条件としての安定供給が必要です。今回の活動が、その助けになっていくと思います。今後の定期修理時の在庫準備にも力を発揮してくれると期待しています」と、今後の展開を口にします。
かつてのSAPは大量に吸水することが重視されていましたが、様々な機能が付加された製品へと変化を続けています。そんな変化に対応するために、日本触媒では多くの部署が連携し合って、SAPの製造技術を進歩させています。
SAPは世界中の人々にとって毎日の生活に欠かせないものです。その期待に応えるため、私たち日本触媒は、紹介したような生産活動や改善活動を通じて、これからも日々進化を続けていきます。